In the realm of industrial grinding, precision is paramount. The effectiveness of grinding processes hinges on the quality and uniformity of the grinding media balls employed. To address this, automatic separating and sorting equipment has become indispensable, offering the ability to classify and segregate grinding media balls based on specific sorting criteria. In this article, we explore the pivotal role of sorting criteria in automatic separating and sorting equipment and its impact on enhancing grinding efficiency.
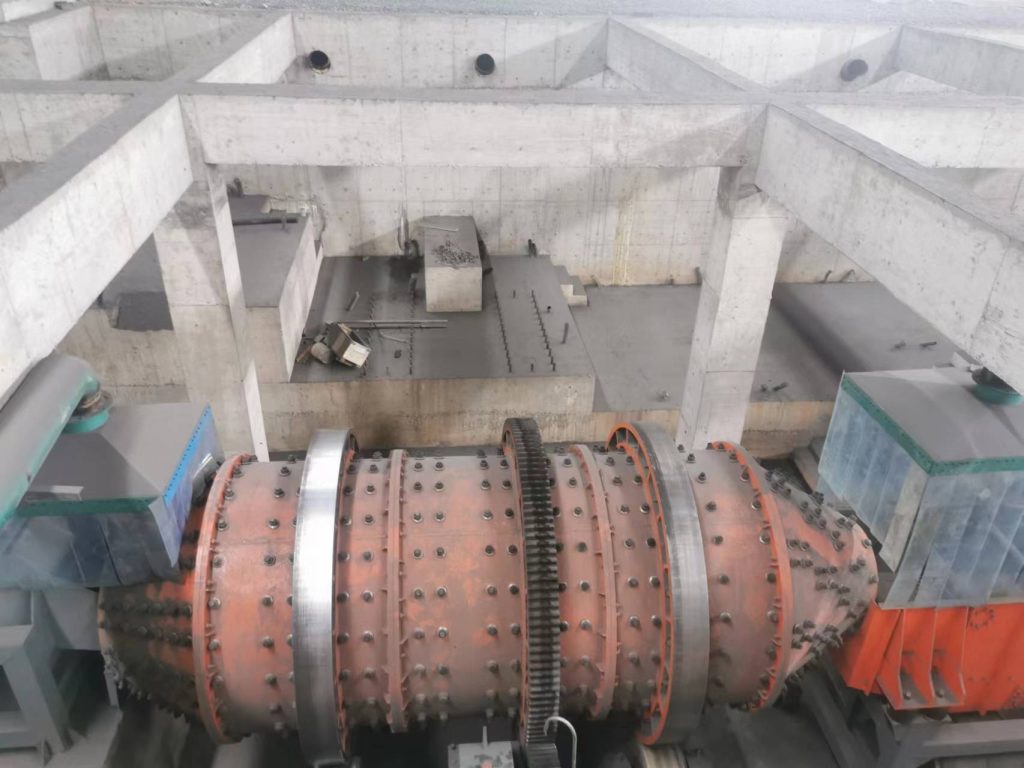
Understanding Sorting Criteria:
Automatic separating and sorting equipment for grinding media balls relies on various sorting criteria to categorize and separate the balls effectively. These criteria encompass:
Size:
Size serves as a fundamental sorting criterion, allowing equipment to categorize grinding media balls based on their diameters. Ensuring uniformity in size facilitates consistent grinding performance and particle size reduction.
Shape:
The shape of grinding media balls can vary, ranging from spherical to irregular shapes. Automatic sorting equipment distinguishes between different shapes, enabling the selection of balls suited for specific grinding applications.
Density:
Density plays a crucial role in sorting grinding media balls, as balls with different densities may exhibit distinct grinding characteristics. Automatic sorting equipment accurately identifies balls with varying densities, optimizing grinding efficiency.
Surface Quality:
Surface quality influences the performance and longevity of grinding media balls. Automatic sorting equipment detects surface defects and irregularities, ensuring that only balls with impeccable surface quality are utilized for grinding processes.
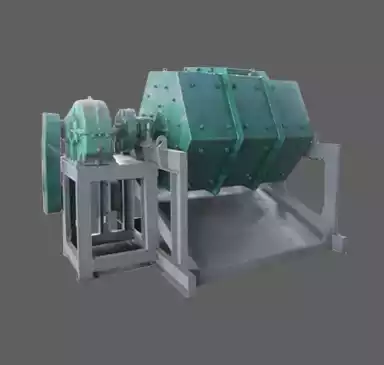
Significance of Sorting Criteria in Grinding Efficiency
The application of sorting criteria in automatic separating and sorting equipment significantly enhances grinding efficiency:
Optimized Grinding Performance: Sorting criteria such as size, shape, density, and surface quality contribute to optimized grinding performance by ensuring the selection of appropriate grinding media balls. This leads to improved particle size reduction and product quality.
Reduced Energy Consumption: By eliminating undersized or oversized balls and those with irregular shapes or surface defects, automatic sorting equipment minimizes energy consumption associated with inefficient grinding. This results in enhanced energy efficiency and reduced operational costs.
Extended Equipment Lifespan: Sorting criteria contribute to the longevity of grinding equipment by removing abrasive or irregular balls that can cause premature wear. This leads to reduced maintenance requirements and prolonged equipment lifespan.
Enhanced Process Control: Automatic sorting equipment provides precise control over the composition of grinding media, allowing operators to adjust sorting criteria as needed. This enhances process control and ensures consistent product quality.
Automatic separating and sorting equipment equipped with sophisticated sorting criteria plays a crucial role in achieving precision and efficiency in grinding processes. By effectively categorizing grinding media balls based on size, shape, density, and surface quality, this equipment optimizes grinding performance, reduces energy consumption, extends equipment lifespan, and enhances process control.
As industries continue to prioritize efficiency and quality in grinding operations, the adoption of advanced sorting criteria in automatic separating and sorting equipment will remain instrumental in driving productivity and competitiveness.