Casting is a widely utilized manufacturing process that involves pouring molten metal into a mold to create intricate shapes and components. To achieve superior casting quality, it is crucial to carefully control various parameters, including the pouring rate and temperature. In this article, we will delve into the impact of these factors on the casting process and highlight advanced control techniques to optimize them for exceptional casting quality.
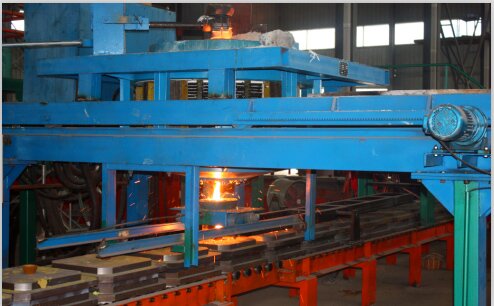
The Role of Pouring Rate:
The pouring rate, or the speed at which molten metal is introduced into the mold, plays a pivotal role in determining the overall quality of the final casting. By precisely managing the pouring rate, manufacturers can achieve the following benefits:
a. Enhanced Fillability and Fluidity: Controlling the pouring rate ensures that the molten metal uniformly fills the mold. A slow pouring rate may result in incomplete filling and the formation of defects such as cold shuts or misruns. Conversely, a fast pouring rate may induce turbulence and lead to the entrapment of air or slag, resulting in porosity and other casting defects.
b. Optimized Solidification: The pouring rate significantly affects the solidification pattern of the metal. A slower rate allows for better heat dissipation, reducing the risk of shrinkage defects. Additionally, it promotes directional solidification, aligning the grain structure and improving the mechanical properties of the casting.
c. Minimized Mold Erosion and Splashing: Excessively high pouring rates can cause erosion or damage to the mold cavity due to the forceful impact of the molten metal. This can lead to surface defects and dimensional inaccuracies in the final casting. Splashing of molten metal is also more prone to occur at high pouring rates, increasing the risk of worker injury.
The Influence of Temperature:
The temperature of the molten metal during pouring plays a vital role in the casting process and the quality of the final product. Here are some crucial aspects to consider when managing temperature:
a. Flowability and Fillability: Higher temperatures decrease the viscosity of the molten metal, improving its flowability and fillability, particularly for castings with intricate geometries or thin sections. However, excessively high temperatures can cause rapid oxidation or evaporation of alloying elements, resulting in compositional variations and casting defects.
b. Controlled Solidification and Cooling: The temperature of the molten metal affects the solidification time and cooling rate. Careful control of these factors is crucial to prevent the formation of shrinkage voids, porosity, or cracks. By maintaining proper temperature control, manufacturers can achieve controlled solidification, ensuring a sound and homogeneous microstructure in the casting.
c. Preserving Mold Integrity: The temperature of the molten metal can impact the integrity of the mold. Pouring metal at excessively high temperatures can cause thermal shock, resulting in mold cracking or spalling. It is vital to strike a balance between achieving sufficient fluidity and preserving the integrity of the mold.
Leveraging Advanced Control Techniques:
To optimize the pouring rate and temperature, manufacturers can employ advanced control techniques, such as computer simulations and sophisticated monitoring systems. Computer simulations allow for the prediction of flow patterns and solidification behavior, enabling the determination of optimal pouring rates and temperatures for specific casting designs. Additionally, sophisticated monitoring systems provide real-time feedback on temperature, allowing for precise control and adjustment during the casting process.
By implementing these advanced control techniques, manufacturers can achieve defect-free castings with superior mechanical properties. Optimized pouring rates ensure complete mold filling, promote directional solidification, and minimize defects due to turbulence or entrapped air. Well-managed temperatures enhance flowability, solidification, and cooling, influencing the microstructure and integrity of the casting. Through careful management of the pouring rate and temperature, manufacturers can ensure high-quality castings that meet desired specifications and performance requirements. Unlock the full potential of casting with our expertise in advanced control techniques and achieve exceptional casting quality in your manufacturing processes.
As we conclude our exploration into the critical factors of pouring rate and temperature in casting quality, we invite you to join us at Zhicheng. We take immense pride in being premier manufacturers and exporters of state-of-the-art pouring machines.
Behind our commitment to excellence lies a dedicated team and a cutting-edge manufacturing facility. At Zhicheng, we prioritize not just meeting but exceeding industry standards, ensuring that our pouring machines stand out for their quality and precision.
Embrace a seamless blend of innovation and reliability as you navigate through our diverse range of machinery designed to enhance your casting processes. Whether you prioritize precision, efficiency, or adaptability, our products are engineered to meet your unique requirements.