The casting process involves pouring molten metal into molds to create complex shapes. To ensure accuracy and efficiency, pouring machines are widely used. These machines automate the pouring stage and play a crucial role in the casting industry. This article will explore the working principle of pouring machines and their significance in the casting process.
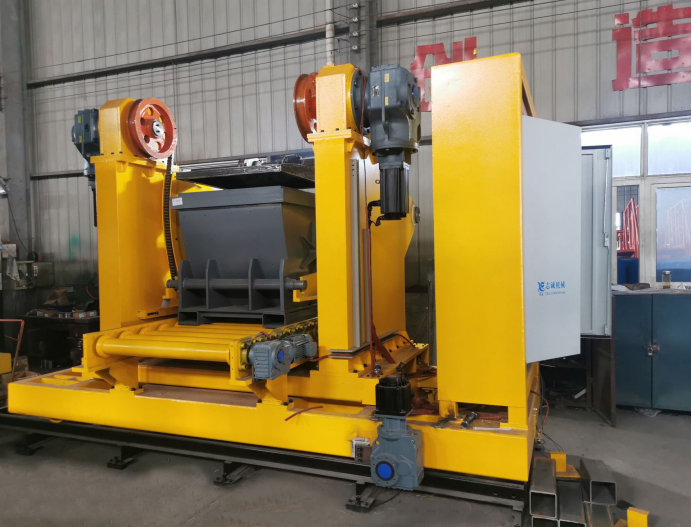
Pouring Machines: Enhancing Casting Efficiency
Pouring machines, also known as automatic pouring systems or robotic pouring machines, are designed to handle the precise pouring of molten metal into mold cavities. They offer numerous benefits, including improved productivity, reduced errors, and enhanced worker safety. Pouring machines are programmable and can be integrated with other automated systems, making them highly versatile.
Working Principle: Consistent and Accurate Pouring
The primary objective of a pouring machine is to consistently and accurately deliver molten metal into molds. Here's how it typically works:
Molten Metal Transfer: The molten metal is initially contained in a ladle, which is positioned near the pouring machine. The ladle may be elevated for gravity-induced flow or connected to a crucible for a pressurized system.
Positioning: The pouring machine is equipped with an articulated arm or a robotic manipulator that precisely positions the ladle above the mold cavity. This ensures precise pouring into the desired location within the mold.
Flow Control: The pouring machine initiates controlled pouring of the molten metal. Flow control mechanisms such as stopper rods, slide gates, or valves regulate the rate and volume of metal being poured, ensuring uniformity and preventing overflow.
Mold Filling: As the molten metal is poured, it gradually fills the mold cavity, taking the desired shape. The pouring machine may oscillate or move in a specific pattern to facilitate even distribution of the metal within the mold.
Monitoring and Feedback: Throughout the pouring process, the pouring machine continuously monitors critical parameters such as temperature, flow rate, and pressure. This data ensures casting quality and allows for adjustments if necessary.
Pouring Completion: Once the mold cavity is adequately filled, the pouring machine stops the flow. The ladle is then returned to its original position, ready for another cycle or replenishment with molten metal.
Pouring machines have revolutionized the casting industry by automating and streamlining the pouring process. Their ability to precisely control the flow of molten metal into molds ensures consistent casting quality, improved efficiency, and enhanced worker safety. As technology advances, pouring machines are expected to become even more sophisticated, enabling foundries to produce high-quality castings with greater precision and productivity.
If you are intrigued by the intricate processes involved in casting and want to explore further, our website offers a treasure trove of information on various casting equipment, including grinding machines, as well as comprehensive production lines. Delve into the vast array of options available and discover innovative solutions that can elevate your casting endeavors to new heights.
Whether you are a seasoned industry professional or a curious enthusiast, our website caters to all levels of interest and expertise. Uncover the latest advancements, gain insights from experts, and stay up-to-date with cutting-edge technologies in the casting industry. Visit our website today and unlock a world of possibilities in casting equipment and production lines.