When it comes to casting processes, selecting the right pouring machine is crucial for achieving efficient and high-quality results. The pouring machine plays a significant role in ensuring precise pouring and consistent casting quality. To make an informed decision when choosing a pouring machine, it’s important to consider several key features that can impact the casting process. Let’s explore these essential features in detail:
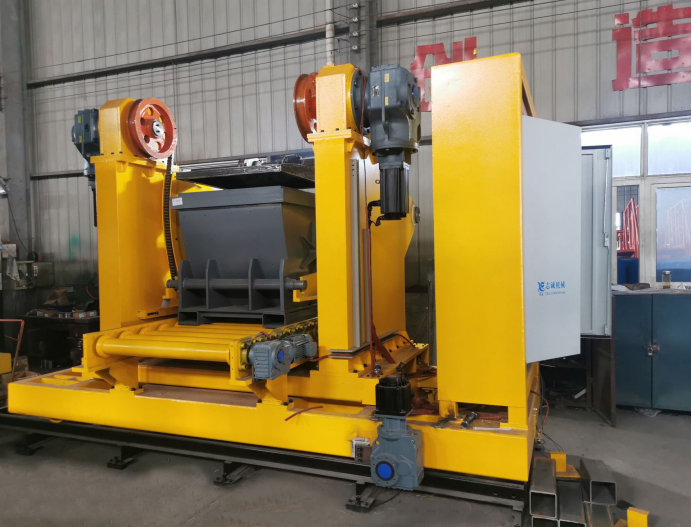
Pouring Capacity:
The pouring capacity of the machine is a critical consideration. It should align with the specific needs of the casting operation, taking into account the volume and size of the castings being produced. Selecting a pouring machine with the appropriate pouring capacity ensures that the production process can run smoothly without bottlenecks or delays.
Control System:
An advanced and reliable control system is essential for precise and automated pouring operations. Look for a pouring machine that offers programmable control features, ensuring accurate pouring rates, consistent metal flow, and the ability to accommodate various casting requirements. A user-friendly interface and the capability to store multiple casting recipes can further enhance operational efficiency.
Pouring Mechanism:
Different pouring machines utilize various pouring mechanisms, such as tilting, bottom pouring, or vacuum-assisted pouring. Consider the specific casting requirements and material characteristics when selecting a pouring mechanism. For example, tilt pouring machines are suitable for casting complex molds, while bottom pouring machines are effective for handling large, solid molds.
Safety Features:
Safety is paramount in any industrial setting, and pouring machines for casting are no exception. Look for features such as automated safety interlocks, splash guards, and emergency stop systems to mitigate potential hazards during the pouring process. Additionally, ensure that the machine complies with relevant safety standards and regulations.
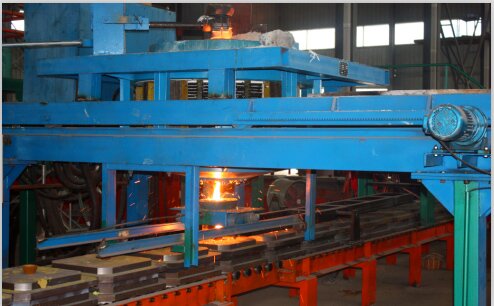
Maintenance and Serviceability:
Selecting a pouring machine that is easy to maintain and service can greatly impact operational uptime and overall cost-effectiveness. Consider machines with accessible components, simple maintenance procedures, and reliable after-sales support from the manufacturer or supplier.
Integration and Compatibility:
If the casting operation uses automated or robotic systems, compatibility with the pouring machine is crucial for seamless integration. Ensure that the pouring machine’s interfaces and communication protocols align with the existing production setup for optimized workflow and data exchange.
In conclusion, selecting the right pouring machine for casting involves careful consideration of several key features. From pouring capacity and control systems to safety features and maintenance considerations, each feature plays a critical role in determining the efficiency and effectiveness of the casting process. By taking these features into account and conducting thorough research, manufacturers can make informed decisions to enhance their casting operations with the optimal pouring machine.
Ensuring that the pouring machine aligns with the specific needs of the casting operation will ultimately contribute to improved productivity, casting quality, and overall operational success. By investing in a pouring machine that offers the right features, manufacturers can streamline their casting processes and achieve exceptional results.